Die Teams der Rennserie „Formula Student“ versuchen jede Saison aufs Neue sich durch Neukonstruktionen und Optimierungen an ihrem Fahrzeug Vorteile gegenüber den Wettbewerbern zu verschaffen. Mit dem Versuch bei ihrem Rennwagen das Fahrwerk erstmalig durch die leere Motorhaube zu führen, stand das Studenten-Team der Ostbayerischen Technischen Hochschule Amberg-Weiden vor der Frage, wie der Stab des Fahrwerksstabilisators befestigt werden könnte. Um den Arbeitsaufwand und das Gewicht des Rennwagens so gering wie möglich zu halten und gleichzeitig die nötigen Toleranzen zu gewährleisten, entschieden sich die Studenten für eine Lösung aus dem 3D-Drucker. Das passende abriebfeste Filament für eine schmier- und wartungsfreie Bewegung kam dabei von dem motion plastics-Spezialisten igus.
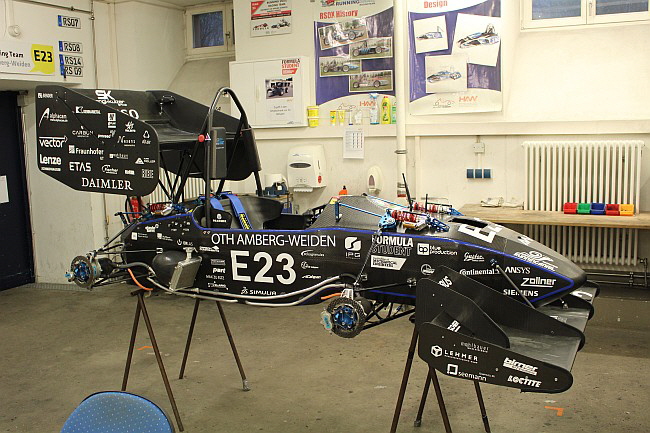 Der Rennwagen des Formula Student Teams Running Snail der OTH Amberg-Weiden für die Saison 2015
Die Formula Student ist ein Konstruktionswettbewerb für Studenten, bei dem sich zum einen Teams aus der ganzen Welt mit selbstkonstruierten Fahrzeuge in Rennen untereinander messen; zum anderen geht es für die Teilnehmer darum, sich neben dem theoretischen Studium bereits vor dem Start ins Berufsleben praktisch mit technischen Problemstellungen auseinander zu setzen. Für die Studenten bietet sich also die Chance, intensive Erfahrungen in Konstruktion und Fertigung, Teamwork, Zeit- und Projektmanagement sowie den wirtschaftlichen Aspekten des Automobilbaus zu sammeln und so ihre fachlichen Qualifikationen zu steigern.
Bessere Chancen durch Gewichtsreduzierung Neben diesen Aspekten sehen die Teilnehmer des Rennteams „Running Snail“ der OTH Amberg-Weiden den eigentlichen Geist der Formula Student jedoch in der Kreativität bei der Suche nach neuen Lösungen. „Da man sich von Saison zu Saison weiterentwickeln muss, steht man häufig vor der Frage wie sich beispielsweise das Gewicht als wichtigster Faktor weiter reduzieren und die Leistung des Wagens gleichzeitig steigern lässt“, so Thomas Faltermeier, technischer Leiter des Teams in der Saison 2015. Diese mit vielen Tests verbundene „Tüftelei“ stellt für ihn den spannendsten Teil des Wettbewerbs dar.
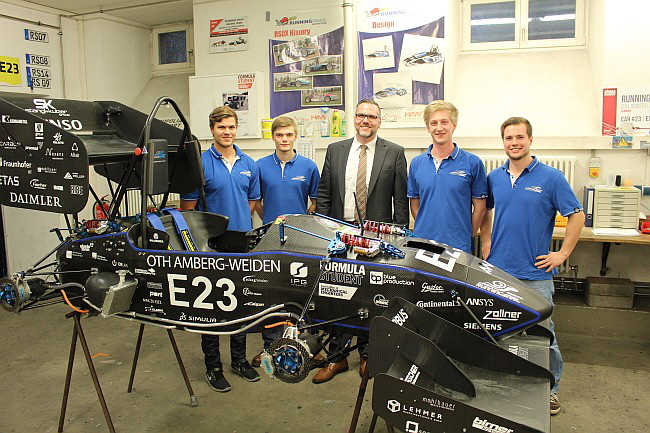 Gemeinsam entwickelten sie die neue Konstruktion des Fahrwerksstabilisators. Von links nach rechts: David Bürner, Philipp Hagn, Rudolf Buchner, Dominik Neuhardt, Thomas Faltermeier
Gerade bei solchen Projekten versucht der motion plastics-Spezialist igus aus Köln mit seinem Know-How und durch die Bereitstellung von kostenfreien Mustern zu unterstützen. Mit dem so genannten ‚young engineers support‘ (kurz ‚yes‘) stellt igus Schülern und Studenten sowie Lehrern, Dozenten oder Professoren sowohl kostenlose Muster seiner Produkte als auch individuell auf ihre Bedürfnisse zugeschnittenes Anschauungs- und Infomaterial zur Verfügung.
Immer neue Anwendungen dank regelmäßigem Austausch Den ersten Kontakt zu igus hatte das Team Running Snail bereits in der Saison 2011/2012. „Die regelmäßigen Treffen zur Neuheitenpräsentation standen im Zeichen, durch neue Produkte Gewicht zu sparen und Wartungsaufwand zu reduzieren“, erklärt Faltermeier. So wurden in den letzten Jahren bereits zahlreiche Anwendungen mit gewichtssparenden und schmiermittelfreien iglidur Gleitlagern und igubal Gelenklagern, beispielsweise in den Stabilisatoren vorne und hinten, gelöst. Seit 2013 befindet sich außerdem eine drylin Lineareinheit zur Verstellung der Pedalerie im Rennwagen (Bild 5).
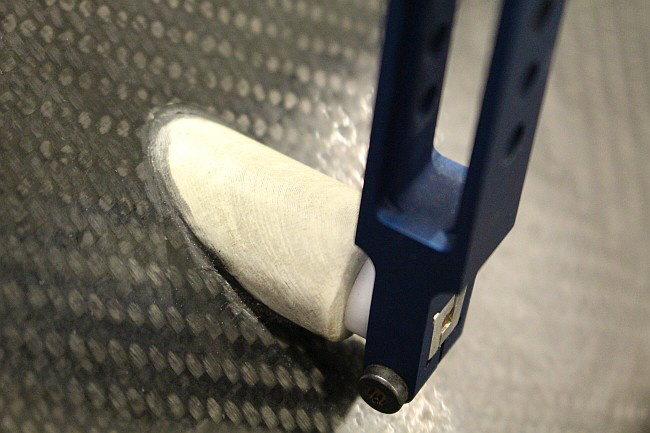
Für die Saison 2015 konzentrierten sich die Studenten auf das Fahrwerk. Dieses wurde erstmalig so weit oben verbaut, dass der Stab des Fahrwerksstabilisators durch die leere Haube geführt werden und eine Kraft von 1000 Newton aushalten muss. Dementsprechend suchte das Team nach einer Lösung dafür, den für das Auspendeln beider Achsen verantwortlichen Stab anzubringen. Erste Überlegungen führten hierbei zu einer verschweißten Lösung, die jedoch aufgrund des zusätzlichen Gewichts, des zeitintensiven Arbeitsaufwands und der fehlenden Toleranzen aufgrund des Schweißverzugs schnell wieder verworfen wurde. Auf die passende Lösung kamen die Studenten durch den letzten Termin mit igus. So erinnerten sich die Studenten an das damals neu vorgestellte iglidur Tribo-Filament I170-PF, welches von Beginn an begeisterte; die passende Anwendung fehlte jedoch bisher. Gerade die Freiheit in der Konstruktion von Einzelteilen oder Prototypen will igus nämlich mit seinem 2014 vorgestellten Filament für den 3D-Druck erleichtern. Als Ergebnis unzähliger Tests im hauseigenen 2.750 Quadratmeter großen Testlabor bietet der Kölner Kunststoffspezialist mit dem weltweit ersten Tribo-Filament einen 50-mal abriebfesteren Werkstoff im Vergleich zu herkömmlichen 3D-Druckmaterialien. Die ersten Muster durfte das Team dann im hochschuleigenen Werkzeugmaschinenlabor unter der Leitung von Professor Wolfgang Blöchl drucken und konnte so mit den passenden CAD-Daten den Arbeitsaufwand minimieren. Nach diversen Versuchen, anschließendem Nachbearbeiten für eine gleichmäßige Oberfläche und der Verklebung am Auto bestanden jedoch zunächsteinige Zweifel hinsichtlich der Steifigkeit und Festigkeit des Lagers zur Führung des Stabilisators. Denn durch unregelmäßige und unterschiedlich starke Stöße aufgrund von Unebenheiten auf der Rennstrecke müssen nicht nur die Torsionssteifigkeit und Festigkeit, sondern auch die entsprechenden Toleranzen gegeben sein. Trotz dieser anfänglichen Zweifel ist das Lager nun aber seit über einem Jahr ohne Ausfall erfolgreich im Einsatz.
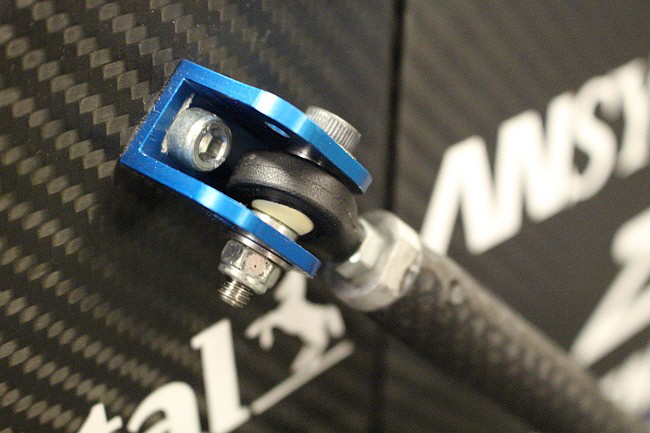 Viele weitere Produkte von igus finden ihren Platz in dem Rennwagen des Teams Running Snail. Hier: igubal Gelenklager an der Anbindung des Frontwings.
Jetzt neu: Sonderteile auch ohne 3D-Drucker schnell geliefert Wem jedoch nicht wie dem Team Running Snail ein 3D-Drucker zur Verfügung steht, dem bietet igus dennoch die Möglichkeit das iglidur Tribo-Filament zu nutzen. So ergänzt igus jetzt sein Angebot um einen 3D-Druckservice (www.igus.de/3DDruckservice) und übernimmt die komplette Herstellung von Sonderteilen. Des Weiteren können Besonderheiten, beispielsweise zur mechanischen Nachbearbeitung, ergänzt werden. Die Dauer beträgt vom Auftragseingang bis zur Auslieferung der fertigen Produkte in der Regel zwei bis drei Werktage, je nach Umfang der Bestellung. Bei komplexen Bauteilen kann die Lieferzeit unter Umständen weitere zwei bis drei Tage betragen. Der Service für Kunden bis zum fertigen Bauteil wird dabei so einfach wie möglich gestaltet. So können über die igus-Website mit nur wenigen Klicks die CAD-Dateien hochgeladen, das richtige Material ausgewählt, mit Preisen eingesehen und die Produkte bestellt werden. Außerdem hat igus sein Angebot rund um den 3D-Druck weiter ausgebaut und jetzt das erste SLS-Material iglidur I3-PL vorgestellt. Mit der gewohnten Verschleißfestigkeit von iglidur-Werkstoffen können Kunden ab sofort auch Sonderteile und Prototypen speziell für bewegte Anwendungen im selektiven Lasersintern fertigen. Sehr komplexe Formen und eine hohe Genauigkeit der Bauteile sind dadurch möglich – und das bei mindestens dreimal höherer Abriebfestigkeit im Vergleich zu anderen SLS-Materialien.
Von diesem Service können zukünftig auch Formula Student-Teams und Studentenprojekte profitieren, denen die Benutzung eines 3D-Druckers nicht möglich ist. Die Mitglieder des Teams Running Snail jedenfalls sind mit dem Ergebnis sehr zufrieden und planen bereits die Anwendung einer weiteren igus-Neuheit zur Gewichtsreduktion.
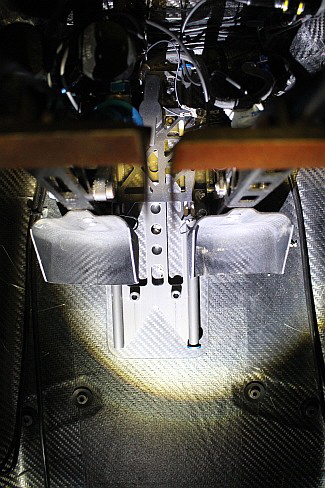 Zur Verstellung der Pedalerie wurde auch eine drylin-Lineareinheit verbaut
Über igus Die igus GmbH ist ein weltweit führender Hersteller von Energiekettensystemen und Polymer-Gleitlagern. Das familiengeführte Unternehmen mit Sitz in Köln ist in 35 Ländern vertreten und beschäftigt weltweit über 2.950 Mitarbeiter. 2015 erwirtschaftete igus mit motion plastics, Kunststoffkomponenten für bewegte Anwendungen, einen Umsatz von 552 Millionen Euro. igus betreibt die größten Testlabore und Fabriken in seiner Branche, um dem Kunden innovative auf ihn zugeschnittene Produkte und Lösungen in kürzester Zeit anzubieten.
|